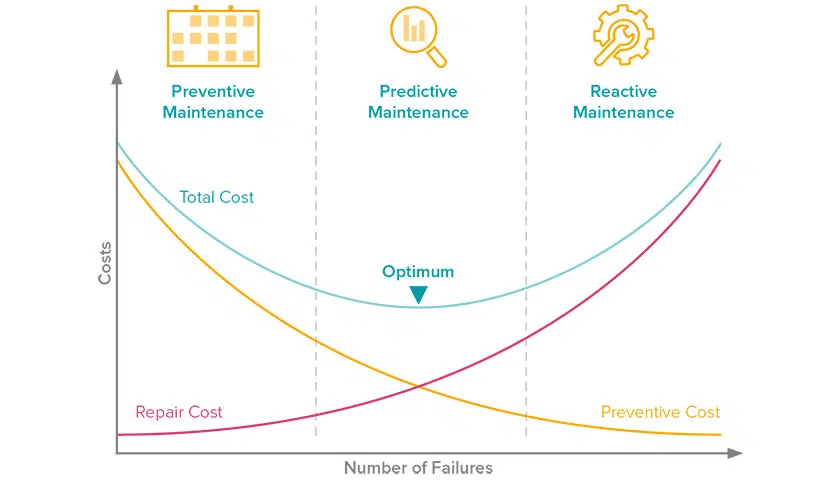
The Hidden Cost of Reactive Maintenance (and Why Predictive Wins Every Time)
Introduction:
Most property owners know the drill: something breaks, you call a contractor, and you foot the bill. But what seems like standard maintenance is actually a high-risk, high-cost approach that eats into your margins and reduces asset longevity.
At Nesos Group, we help clients flip the script with predictive maintenance—using real-time monitoring and smart analytics to detect early warning signs and fix problems before they lead to costly breakdowns. The result? Fewer surprises, lower costs, and smarter asset management.
What Is Reactive Maintenance And Why Is It a Problem?
Reactive maintenance (also known as “run-to-failure”) means waiting until something fails before addressing it. It might seem efficient in the short term, but the hidden costs quickly pile up:
- Emergency call-out fees
- Equipment downtime
- Unplanned disruptions to tenants or business
- Shorter asset lifespan
- Higher insurance claims and premiums
“Reactive maintenance can cost 2–5x more than proactive alternatives, once labour, downtime, and secondary damage are considered.”
– U.S. Department of Energy, 2023
Why Predictive Maintenance Is the Smarter Alternative
Predictive maintenance uses smart sensors, data analytics, and machine learning to monitor system performance in real time. These tools identify signs of wear, inefficiency, or failure before it happens, allowing for:
- Scheduled interventions
- Lower repair costs
- Maximised equipment life
- Reduced operational risk
The Hidden Costs of Reactive Maintenance (With Real-World Impact)
1. Emergency Repair Premiums
When a system fails outside of regular hours, you’re often paying 50–100% more for labour and expedited parts.
Example:
A reactive HVAC call-out might cost £1,000–£1,500.
A proactive repair caught early might cost £250–£400.
2. Collateral Damage
One small fault can quickly escalate. A leaking pipe left for a week might cause mould, flooring damage, or electrical issues, multiplying costs and insurance headaches.
“60% of insurance claims from water damage could have been avoided with early detection.”
– Insurance Business UK, 2023
3. Equipment Replacement
Reactive maintenance shortens the lifespan of systems like boilers, chillers, HVAC, and pumps. Preventive attention keeps components clean, aligned, and running at spec.
Cost impact:
Replacing a failed chiller unit: £20,000–£50,000
Extending its life by 5 years: savings of 40–60%
4. Downtime and Disruption
Whether it’s a hotel losing rooms, an office block with no cooling, or a tenant without hot water – downtime costs money and damages your reputation.
Tenant retention suffers, and occupancy rates can drop as a result.
5. Compliance Risk and Insurance Claims
Reactive systems often fail to meet service interval requirements. This can trigger compliance violations or void insurance claims if the insurer deems the issue was due to “neglect” or “lack of maintenance.”
How Predictive Maintenance Works in Practice
At Nesos Group, our predictive systems monitor:
- HVAC performance and airflow
- Water temperature and flow rates
- Boiler pressure and cycle rates
- Motor vibrations and electrical usage
- Humidity and environmental data
When anomalies are detected (e.g., rising vibration, inefficient burner cycling), our team is alerted and schedules intervention-often avoiding a full failure entirely.
“Predictive maintenance reduces unplanned downtime by up to 50% and extends equipment life by 30–40%.”
– McKinsey & Company, 2023
Implementation: How to Move From Reactive to Predictive
Step 1: System Audit
Identify high-risk, high-cost systems in your property – typically HVAC, pumps, boilers, and water systems.
Step 2: Install Smart Sensors
Deploy vibration, flow, temperature, and energy usage monitors in key zones.
Step 3: Set Threshold Alerts
Configure real-time alerts for performance anomalies and inefficiencies.
Step 4: Plan Proactive Interventions
Create workflows for scheduled inspections or part replacements before failures occur.
Step 5: Optimise and Report
Use dashboard insights to refine scheduling, plan capital expenditures, and strengthen insurance claims.
Conclusion
If you’re still waiting for things to break before fixing them, you’re not managing your property-you’re gambling with it.
With predictive maintenance, Nesos Group helps owners reduce emergency costs, extend asset life, and avoid disruption – making property care intelligent, proactive, and cost-effective.
“In property management, the most expensive repairs are the ones you didn’t see coming.”
– Nesos Group Insight, 2025
What an incredible first week it has been for Nesos Group! Our intelligent property management platform has already attracted some amazing attention, and we couldn’t be more excited.
The response from our wonderful island community has been truly overwhelming—in the best way possible. Your kind words, support, and enthusiasm mean the world to us as we embark on this journey.
We created Nesos Group to bring innovation and efficiency to property management, and seeing our vision resonate with so many of you is both humbling and inspiring.
A huge thank you to everyone who has reached out, shared their excitement, and welcomed us so warmly. We can’t wait to continue growing, improving, and making a meaningful impact together.
Stay tuned—there’s so much more to come!
The Nesos Group Team